Watch Movement Materials: From Brass to Gold Plating
The intricate world of watch movements is a fascinating blend of engineering precision and craftsmanship. While the design and complexity of these tiny machines are captivating, the materials used to construct them are equally important. Understanding the materials used in watch movement construction – from the ubiquitous brass to the luxurious gold plating – provides deeper insight into a timepiece’s quality, history, and ultimately, its value. This article will explore the common materials found within mechanical watches and their respective roles.
The Foundation: Brass and Bronze
The vast majority of watch movement components are made from brass. Brass is an alloy of copper and zinc, chosen for several key reasons. Primarily, it’s relatively easy to machine, allowing for the creation of the hundreds of intricate parts that comprise a typical watch movement. Its corrosion resistance, while not exceptional, is adequate for most applications. Furthermore, brass is readily available and relatively inexpensive, contributing to cost-effective production.
Different grades of brass exist, each with varying proportions of copper and zinc, influencing its properties. "High-brass" contains more copper, offering improved strength and corrosion resistance, while "low-brass" is softer and easier to machine. Specific alloys are often chosen for particular components based on their required characteristics. For example, the mainspring housing, which is under significant stress, would likely be made from a stronger brass alloy.
Bronze, another copper alloy (typically with tin), is sometimes used in watch movements, particularly in older timepieces. Bronze offers superior corrosion resistance compared to standard brass, making it a good choice for marine chronometers and movements intended for harsh environments. Its use is less common today due to its higher cost and slightly more challenging machining characteristics.
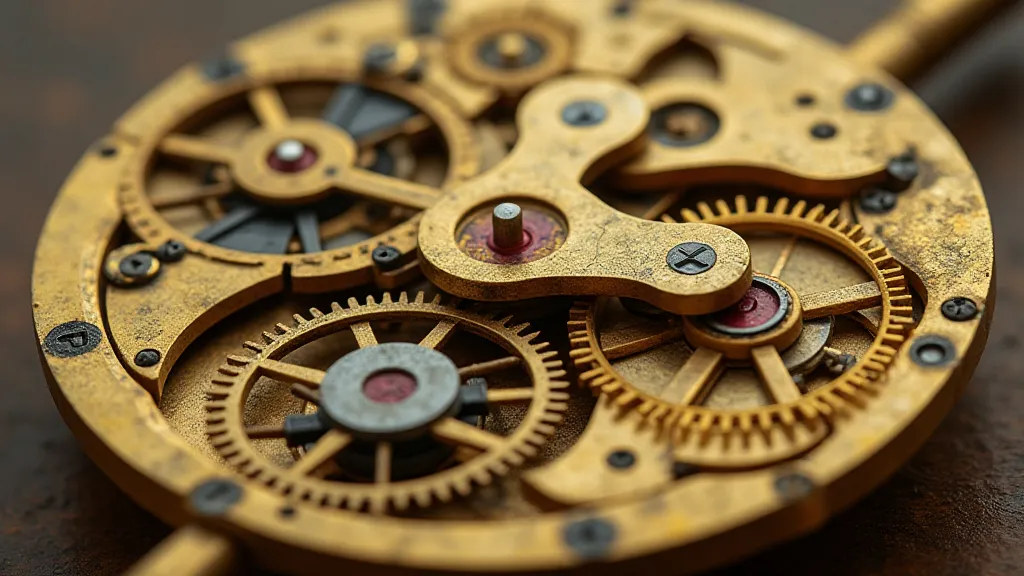
The Strength and Durability of Steel
While brass forms the bulk of a movement’s structure, steel plays a vital role in ensuring strength and durability. Steel, an alloy of iron and carbon, is significantly stronger than brass and offers superior wear resistance. It's crucial for components subjected to high stress, such as the balance spring, pallet fork, and escape wheel.
Different types of steel are used in watch movements. Stainless steel, containing chromium, is highly resistant to rust and staining, making it ideal for visible parts and those constantly exposed to lubricants. Hardened steel, treated with heat to increase its strength, is used for components like the mainspring and gear train. Spring steel, with a unique composition and processing, is specifically designed for the balance spring, requiring exceptional elasticity and stability.
The use of steel in watch movements evolved over time. Early movements almost exclusively relied on brass, but as manufacturing techniques advanced and the demand for more robust timepieces grew, steel became increasingly prevalent. Modern high-end movements frequently utilize a significant percentage of steel components, particularly those critical to accuracy and reliability. To better understand the ongoing evolution and future trends impacting these complex systems, consider exploring the future of watch movements.
Precious Metals: Gold, Silver, and Their Alloys
While brass and steel dominate the internal workings of most watch movements, precious metals often feature in more luxurious and historically significant timepieces. Gold, in particular, has long been associated with high-end watchmaking, used for plating, decoration, and even the construction of entire movements.
Gold's inherent softness makes it unsuitable for structural components in its pure form. However, it's commonly alloyed with other metals like silver, copper, and zinc to improve its strength and durability. The proportion of gold in the alloy dictates its karat rating – 24 karat being pure gold, and 14 or 18 karat being alloys with a higher proportion of other metals.
Gold plating is a common technique for enhancing the aesthetics of watch movements. A thin layer of gold is applied to a brass base, providing a luxurious appearance and improved corrosion resistance. While not as durable as solid gold, gold plating adds a touch of elegance and prestige to a timepiece.
Silver, while less common than gold, also appears in watch movements, often in the form of delicate engravings or as a base metal for plating. Its bright luster and malleability make it suitable for decorative purposes.
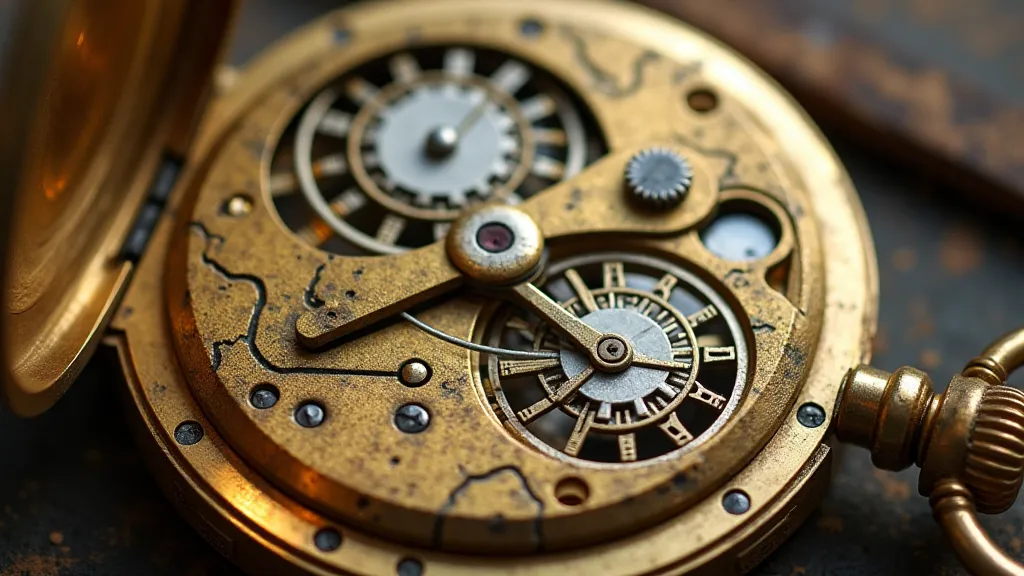
Beyond the Basics: Lubricants and Other Materials
The materials discussed above represent the primary components of a watch movement. However, several other materials play crucial supporting roles. Lubricants, such as oils and greases, are essential for reducing friction and wear between moving parts. These lubricants are often synthetic compounds designed for extreme precision and long-term stability.
Synthetic rubies or sapphires are frequently used as bearing surfaces for the axles of gears and levers. Their hardness and low friction coefficient ensure smooth operation and longevity. These synthetic gemstones are a testament to the ingenuity of watchmakers and their commitment to precision.
Finally, materials like plastic and rubber may be found in smaller components such as gaskets, seals, and straps, providing protection and ensuring a comfortable wearing experience.
Understanding Movement Identification and Serial Numbers
The precise identification of a watch movement is crucial for collectors and enthusiasts alike. Movement serial numbers, while often seemingly random, offer valuable insights into a movement's production date, origin, and even its intended application within a specific watch model. Understanding how to decode these numbers can unlock a wealth of information about your timepiece's history and authenticity. For a deeper dive into understanding these serial numbers and what they can reveal, you can find more details on understanding watch movement serial numbers.
Regional Differences and Specialized Movements
It’s important to note that the materials and construction techniques used in watch movements can vary significantly depending on the manufacturer and region of origin. Japanese movements, for instance, are often known for their innovative use of materials like silicon, while Swiss movements frequently prioritize traditional craftsmanship and the use of high-grade steel and precious metals. Some manufacturers even develop specialized movements tailored to specific applications, such as chronographs, perpetual calendars, or tourbillons.
The Role of Seiko’s Movements and Their Calibers
Seiko, a prominent name in the watchmaking industry, employs a diverse range of movements, each with its own characteristics and strengths. From the ubiquitous 4R series to the more advanced 7S and 6R calibers, Seiko’s movements represent a blend of innovation and reliability. Understanding the nuances of these movements is key to appreciating the quality and value of Seiko timepieces. If you're looking to differentiate and identify various Seiko movements, you can find a helpful guide on Seiko movement identification.
Beyond the Traditional: Emerging Materials and Technologies
The quest for improved accuracy, efficiency, and durability continues to drive innovation in watch movement materials. While traditional materials like brass, steel, and precious metals remain essential, researchers and engineers are constantly exploring new possibilities. Titanium, with its lightweight and corrosion-resistant properties, is finding increasing use in cases and components. Silicon, in the form of silicon balance springs (SiSpirals), offers exceptional stability and accuracy, largely unaffected by temperature fluctuations or magnetic fields. Ceramic materials, known for their hardness and scratch resistance, are also gaining traction in applications ranging from cases and bezels to gear train components.
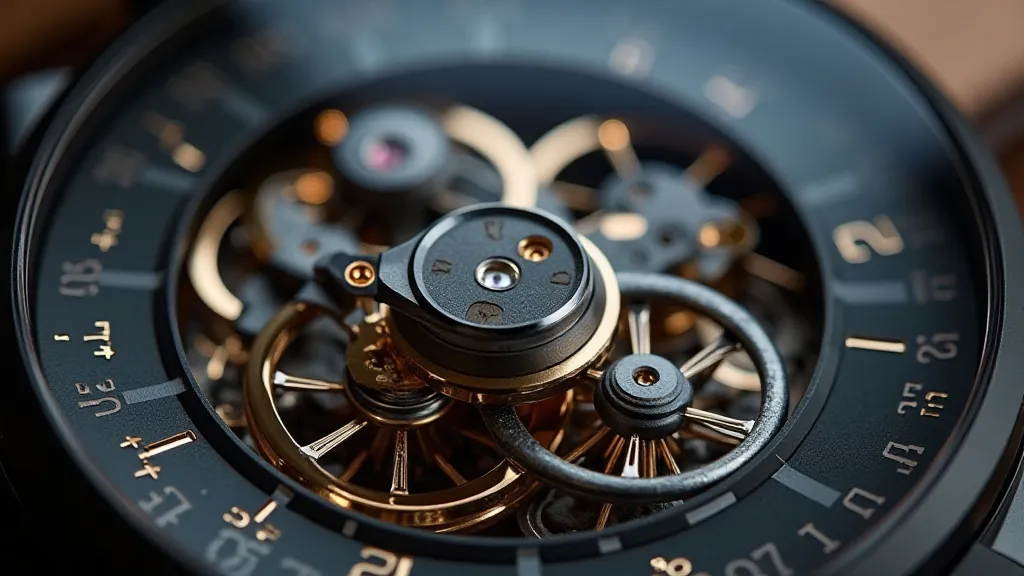
Evolution of Materials and Future Trends
The materials used in watch movement construction have evolved significantly throughout history. Early timepieces relied primarily on brass and iron, with limited use of steel. As manufacturing techniques advanced, steel became more prevalent, and precious metals were incorporated for aesthetic and functional enhancements.
Today, watchmakers are continually exploring new materials to improve performance and efficiency. Titanium, with its lightweight and corrosion-resistant properties, is increasingly used for cases and components. Silicon, in the form of silicon balance springs (SiSpirals), offers exceptional stability and accuracy. Ceramic, with its hardness and scratch resistance, is finding applications in cases, bezels, and other components.
The future of watch movement materials likely holds further innovations, driven by the pursuit of greater accuracy, durability, and sustainability. As watchmaking continues to evolve, we can expect to see even more sophisticated materials integrated into these intricate mechanical masterpieces. This ongoing process of evolution and refinement underscores the enduring ingenuity of watchmakers and their unwavering commitment to pushing the boundaries of horological innovation.
Conclusion
The materials used in watch movement construction are a testament to the ingenuity and craftsmanship of watchmakers. From the common brass to the luxurious gold plating, each material plays a critical role in the functionality, durability, and aesthetic appeal of a timepiece. Understanding these materials provides a deeper appreciation for the complexity and artistry of mechanical watches and offers valuable insight into their history and value. Whether you are a seasoned collector, a budding enthusiast, or simply curious about the inner workings of a watch, exploring the world of watch movement materials is a rewarding journey.