Watch Movement Decoration: From Geneva Stripes to Perlage
The intricate world of watchmaking extends far beyond mere timekeeping. For horological artisans, a significant aspect of creating a truly exceptional timepiece lies in the meticulous decoration of the movement. This isn't simply about aesthetics; it’s a testament to the skill, dedication, and patience of the watchmaker. Decorative techniques enhance the beauty of the movement and, in many cases, serve as an indicator of quality and heritage. This article explores some of the most common and captivating decorative techniques used on watch movements, diving into their history, execution, and significance.
Why Decorate? A History of Adornment
While functional accuracy was paramount for centuries, the tradition of decorating watch movements has roots in both pride of craftsmanship and a desire to showcase technical prowess. Early watchmakers, often working for royalty or wealthy patrons, saw decoration as a way to demonstrate their artistry and justify their high fees. As watchmaking matured, some decorations became indicators of prestige. More elaborate and time-consuming decorations were generally found in higher-grade watches, signaling a commitment to excellence. The rise of industrialization initially threatened to eliminate these artisanal skills, but a renewed appreciation for traditional craftsmanship, especially in Swiss watchmaking, spurred a resurgence in decorative techniques. It’s fascinating to consider how the very design and layout of a movement often reflects the prevailing aesthetic and technological constraints of its era – a subject explored further in The Echo of Hammers: How Movement Design Reflects the Soul of its Era.
Today, decorated movements are found in a wide range of timepieces, from entry-level mechanical watches to ultra-luxury creations. While some manufacturers prioritize function and affordability, others view movement decoration as an integral part of their brand identity and a selling point for discerning collectors.
Geneva Stripes (Côtes du Geneve)
Perhaps the most recognizable decorative technique, Geneva stripes, also known as Côtes du Geneve, is characterized by parallel, hand-laid lines radiating from the central pivot holes of the bridges and plates. The name originates from the Geneva region of Switzerland, a historic center for watchmaking.
Executing Geneva stripes is a remarkably challenging process. It begins with the watchmaker using a hand-operated engine lathe with a toothed cutting tool. The tool is carefully guided across the surface of the component, creating precisely spaced, slightly raised lines. The angle of the tool and the pressure applied determine the depth and prominence of the stripes. The result is a visually striking pattern that catches the light and adds depth to the movement.
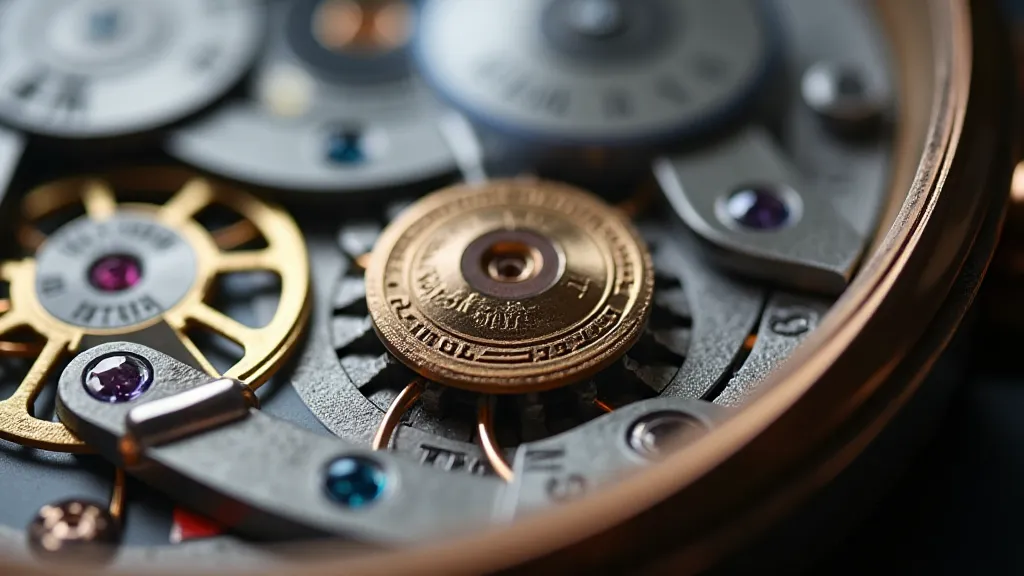
Perlage (Circular Graining)
In contrast to the linear nature of Geneva stripes, perlage involves applying a delicate, circular graining to the surfaces of the movement’s components. The name comes from the Italian word for 'pebbles,' reflecting the appearance of the finished surface. It's also sometimes referred to as undulation.
Perlage is created using a rose engine, a complex machine that produces repetitive geometric patterns. The watchmaker selects a cutting tool and carefully rotates it against the surface of the component, creating a series of overlapping circles. The process requires a steady hand and a keen eye to ensure evenness and consistency. A well-executed perlage finish provides a subtle shimmer and a feeling of understated elegance.
Chamfering
Chamfering refers to the beveled edges of movement components. It's a seemingly simple technique but demands exceptional precision. The edges of bridges, plates, and other parts are angled, typically at 45 degrees, using specialized tools. The resulting facets reflect light in a unique way, adding depth and dimension to the movement. The quality of the chamfering – the sharpness of the edges, the consistency of the angle – is a key indicator of the level of craftsmanship.
Often, chamfering is combined with other decorative techniques, such as Geneva stripes or perlage. The contrast between the beveled edges and the textured surface creates a visually compelling effect.
Anglage (Mirror Polishing)
Anglage takes chamfering a step further. It involves not only beveling the edges of components but also painstakingly polishing them to a mirror-like finish. This process, often done by hand, requires immense skill and patience. The resulting reflection enhances the perceived depth and complexity of the movement.
Anglage is considered one of the most demanding and time-consuming decorative techniques, and it is almost exclusively found in high-end watches. The ability to consistently produce flawless, mirror-polished edges is a hallmark of true mastery. Identifying the unique characteristics of vintage movements, including the specific decorative techniques employed, can often be a challenging endeavor – a puzzle often requiring careful consideration and detailed analysis. For those captivated by the history of timekeeping and the evolution of these intricate mechanisms, Identifying Vintage Watch Movements: Common Challenges and Tips offers valuable insights and practical guidance.
File Work
File work encompasses a range of techniques that involve using files to create specific patterns or textures on movement components. This can include creating delicate ribs, grooves, or other intricate designs. File work is often used to enhance the visual appeal of bridges and other parts of the movement.
The precision and artistry involved in file work are considerable, as it requires the watchmaker to manipulate the file with a steady hand and a keen eye.
Black Polishing (or Mirror Polishing)
Black polishing, sometimes just referred to as mirror polishing, takes the concept of anglage to its extreme. This involves an incredibly meticulous and lengthy process of polishing a surface to an almost black mirror finish. The goal is to eliminate virtually all surface imperfections, resulting in an almost perfectly reflective surface.
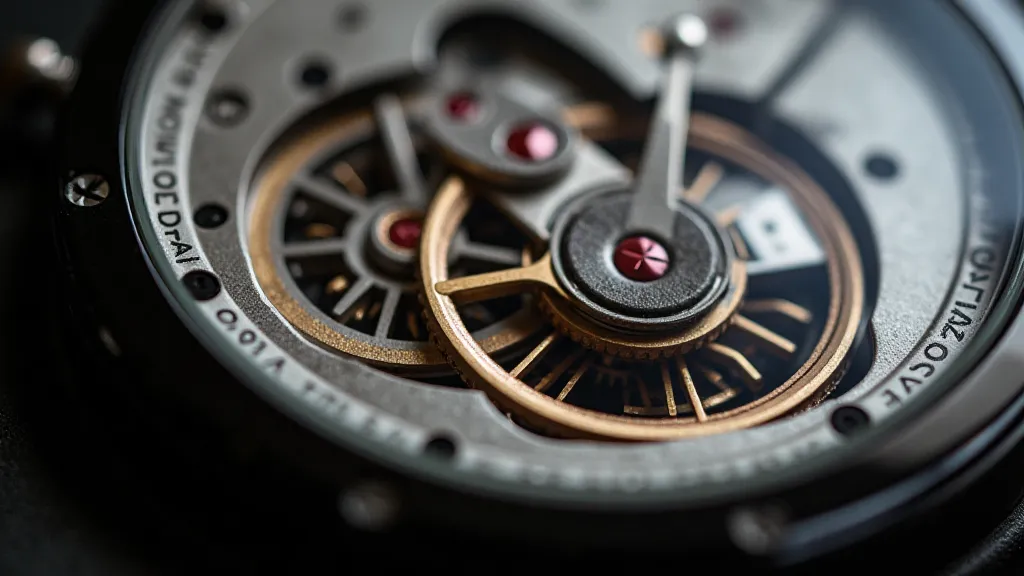
Black polishing requires specialized compounds, tools, and techniques, and it’s typically performed by highly skilled artisans. The result is a truly spectacular finish that elevates the movement’s aesthetics to an exceptional level. The intricate pathways of gears and levers within a watch movement, and the techniques used to adorn them, can be seen as a cartographic representation of time itself – a testament to the ingenious minds who have charted its course. This concept is beautifully explored in The Cartographer of Chronos: Tracing Lost Movements Through History’s Eddies.
The Significance for Watch Collectors
For watch collectors and enthusiasts, appreciating movement decoration goes beyond mere aesthetics. It's a window into the history, tradition, and artistry of watchmaking. The presence of elaborate decorations often indicates a commitment to quality, heritage, and craftsmanship. It’s a tangible expression of the watchmaker’s pride in their work.
Understanding the different decorative techniques allows collectors to better appreciate the value and significance of a timepiece. It provides a deeper connection to the world of horology and a greater appreciation for the dedication and skill required to create a truly exceptional watch.
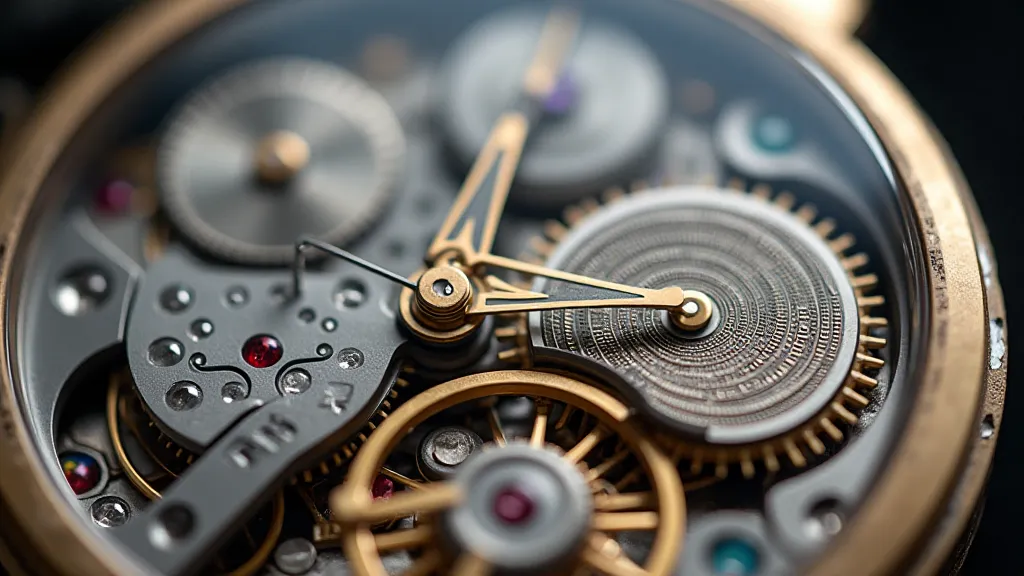
Ultimately, the beauty of a decorated watch movement lies not only in its appearance but also in the story it tells – a story of tradition, innovation, and the enduring pursuit of excellence in watchmaking. It reflects a dedication to preserving time, not just in its measurement, but in its artistry.